Facilities & Equipment
Analytical Equipment and Labs
CPER leverages the world-class analytical capabilities at the UND College of Engineering & Mines.
About Analytical Labs & Equipment
Research Labs
CPER has access to highly flexible and well-equipped wet chemistry labs and high bay labs to facilitate the demonstration of a wide range of process technologies.
- Access to highly flexible and well-equipped wet chemistry labs and high bay labs to facilitate the demonstration of a wide range of process technologies.
- College of Engineering & Mines Drilling & Completions Laboratory / Research Facility, a two-floor 36,000 ft2 high-bay space located off-campus. This is where CPER’s rare earth elements pilot-scale processing plant is located along with several other large research equipment controlled by the College of Engineering & Mines.
Research Equipment
CPER has access to numerous high-temperature furnaces, fixed and fluid bed reaction systems, and sample preparation systems (crushing, milling, sieving) to enable a wide variety of thermochemical process development and testing. In addition, there are several unique equipment available, as described below.
Contact
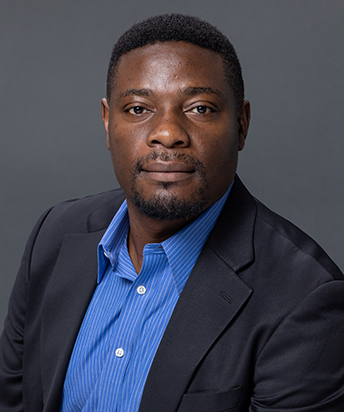
- nasah.domkam@UND.edu
- 701.777.4307
-
Collaborative Energy Complex Room 246F
Grand Forks ND 58202-8153
High-Temperature Bench Gas/Solid Reaction System
CPER is home to two bench-scale, batch, high temperature fixed/fluid bed units that are highly flexible to test a wide range of gas/solid reaction processes under relevant reaction conditions. Typical solid loadings are on the 10s to 100s of grams, within an interchangeable 1-2” reactor vessel. The units are equipped with several reconfigurable mass flow controllers and a steam generator to deliver just about any gas composition desired and can operate at temperatures up to 950°C. These units are also equipped with multi-gas analyzers to measure product gas compositions. Solid particles that escape the main reaction vessel are fully captured on filters to enable mass balance closure and particle characterization.
Down-fired / Drop-Tube Combustor
CPER has access to a 10 kW multi-fuel down-fired combustor capable of firing gases (propane, methane), liquids (glycerin, oils) and powdered solids (coal). The unit (graphic below) is equipped with two solid feeders, an electrically heated combustion zone, multiple sample ports for gas composition or temperature profile and a fabric filter for dust recovery.
Graphitization Furnace
CPER is home to a 3000 °C bench-scale graphitization furnace. It is a vertical top loading furnace with integrated design and heated through induction heating with heating power of 80 kW. The design maximum heating temperature is 3000 °C for 1 hour and continuous working temperature 2850 °C. The usable space for sample graphitization is 200 x 300 mm.
Laboratory Multimode Fluidized Bed Gasifier/Combustor
CPER is home to a bench-scale multi-mode gasifier unit designed to fire up to 5 lb/hr of coarse solid fuels. The unit can be modified to operate as a bubbling, moving, or Sandwich™ unit (multi-mode) for either combustion or gasification applications.
Sorbent Test Unit
Designed for carbon dioxide capture with sorbents, this unit is capable of evaluating sorbents under a packed or fluid bed solids regime. It consists of a temperature-controlled vessel and flow controllers capable of testing direct air conditions (400 ppm CO2), natural gas combustion (~4% CO2) and coal combustion (~8-15%) gas compositions. A steam generator and air preheater facilitate regeneration in inert or steam conditions. The system is also equipped with sensors for monitoring temperature and pressure and gas analyzers to measure inlet and outlet gas compositions.
TFM2 2-Zone Tube Furnace (Across International)
The TFM2 2-Zone 1200°C tube furnace is built with high-quality materials to calcine materials with high- precision temperature control within +/-1°C accuracy and 10 programmable segments. The furnace can be used under vacuum and other gas conditions and its maximum working temperature is up to 1100°C. It is an ideal tool for sintering all types of materials at laboratory-scale.
Kejia KJ-A1200-27L Atmosphere Furnace
This atmosphere furnace can reach 1100˚C working temperature with a 35-step programmable temperature controller. It holds a vacuum down to -85 kPa and pressure up to 80 kPa. The 27-liter chamber size allows for pilot-scale (up to 10 kg) materials preparation. The chamber can work with any desired atmosphere. The one-way inlet and outlet design allow for excessive pressure relief without contaminating the atmosphere.
Gas and Aerosol Sampling and Analysis
CPER is equipped with multiple gas analyzers for measuring CO2, H2, O2, N2, CO and other gases. Examples of analyzers include multiple Laser Gas Analyzers from Atmosphere Recovery Inc.; VA-3000 and PG250 analyzers from Horiba, and Wohler combustion gas analyzers. CPER also is equipped with complete field sampling trains for EPA Method 5 and for aerosol sampling specifically the Dekati® cyclone (10 µm cutpoint), and the 14 stage and 13 stage Dekati® Low Pressure Impactors DLPI+ and DLPI respectively (image below).
KJ-RT1600-2Z-220220 1600°C Two-zone Rotary Tube Furnace (Zhengzhou Kejia Furnace Co. Ltd)
This 8-kW rotary tube furnace is built with a double-layer structure of carbon steel outside shell and alumina fiber lining. The tube is made of alumina ceramic with the size of OD80mm x L1200mm. It is equipped with a two-channel gas mixing system with mass flow meters for atmosphere control. The maximum working temperature is 1600°C with a heating ramp at 0-15°C/min by MoSi2 heating rods. The maximum tilt angle is 15 degrees.
CPER’s battery fabrication and testing capabilities include materials R&D, materials characterization, cell fabrication, and battery testing & battery management systems R&D. A description of some of our unique capabilities is provided below.
Contact
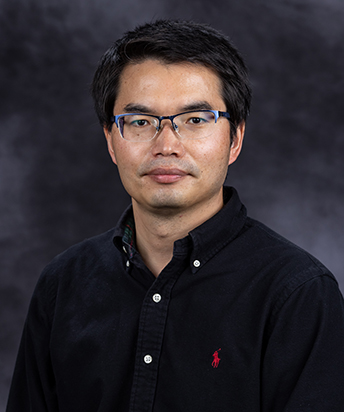
- xiaodong.hou@UND.edu
- 701.777.6350
-
Leonard Hall Room 300
Grand Forks ND 58202-8153
Bench-scale Materials Synthesis
Our bench-scale materials synthesis capabilities include cathode and anode materials such as LiFeSO4, graphite, and silicon, and advanced battery chemistries including Li-S, Na-ion, and solid-state batteries. These facilities are supported by advanced materials characterization equipment including:
- Electrochemical workstation (electrochemical impedance spectroscopy, potentiostat, and galvanostat)
- X-Ray diffractometer (operando/in-situ testing)
- High-resolution Electron Microscopy (scanning electron microscopy and transmission electron microscopy)
- Advanced Synchronize X-ray technology (collaboration with Canadian Light Source)
CPER battery materials synthesis equipment are highlighted below.
- Mixer
- Furnace
- Jet Mill (1-10 kg/h)
- Chemical Vapor Deposition (CVD) Rotary Furnace
Battery Fabrication Equipment
CPER is able to fabricate battery cells including coin cells, pouch-cells and 18650 cells > 2000 mAh. Process steps involved include materials baking, vacuum mixing, electrode coating, large sheet cutting, rolling press, electrode cutting, vacuum drying, glove box, electrolyte filling, crimping machine, and then finally battery testing. Specific pouch-cell and 18650 cell fabrication equipment are highlighted below.
- Coating Machine
- Roll Presser
- Pouch Machine
- Slitting Machine
- Spot Welder
Battery Testing Equipment
CPER has testing capabilities ranging from CR2032 coin-cells to full size 18650 cells and up to 48V battery packs. Testing capabilities include:
- Battery charge/discharge characteristic test
- Battery capacity test
- Battery cycle life test
- Battery filled/discharge efficacy test
- Battery testing with the standard dynamic test
Specific battery testing equipment are highlighted below.
- Gover Box (MBraun LABstar MB10)
- Electrochemical Impedance Spectroscopy (Gamry 1010E)
- Coin-cell Tester (Neware BTS-3000n)
- Large-cell Tester (Neware BTS-4000)
- Pack Tester/Emulator (NHR-9200)
CPER has the capability to perform experimental mineral processing research and development ranging from the lab-scale to large-pilot scale and has fully equipped research labs, supported by advanced analytical labs and experienced chemists, engineers and technicians. The following highlights our team’s bench-scale and pilot-scale critical minerals extraction equipment that has been developed during a series of Department of Energy, State and industry funded projects demonstrating our lignite-based critical minerals technology. These equipment and associated facilities are highly reconfigurable/adaptable to test many types of mineral processing technologies/circuits.
We are actively seeking new partners to leverage these unique facilities.
Contact
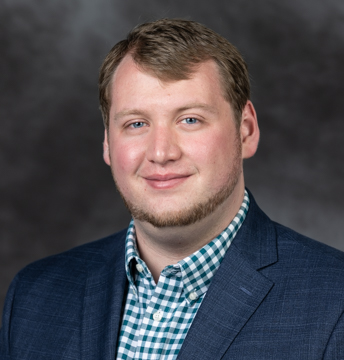
- nolan.theaker@UND.edu
- 701.777.6298
-
Collaborative Energy Complex Room 246C
Grand Forks ND 58202-8153
Bench-scale Equipment
CPER custom designed, fabricated and installed a system that is capable of processing 50 kg batches or ~25 kg/hr of ore. The system includes four reconfigurable 50-gal stirred leach tanks fed by solids feeders (screw conveyors) and chemical dosing pumps, and downstream solid/liquid filtration (filter press) with associated solids and liquid handling/collection systems. The leach tanks are also used for chemical precipitation steps to reject impurities and/or collect desired products. The system is also equipped with an ion-exchange resin column that can perform liquid-phase purification of products. The system is fully instrumented and controlled via a custom National Instruments LabVIEW PLC (see image).
Pilot-scale Equipment
CPER custom designed, fabricated and installed a pilot-scale demonstration facility that is capable of processing 500 kg/hr (nameplate) of ore. The facility covers 10,000 ft2 and includes ore crushing up to 5 tons/hr, physical separation (spirals) and a series of chemical separations. Process areas include:
- Feed handling, preparation and physical separation (spirals),
- Leaching and dewatering
- Impurity precipitation
- Target minerals (e.g. rare earth elements) precipitation, and
- Wastewater collection and treatment.
While this plant was designed specifically to demonstrate our lignite-based critical minerals and rare earth elements technology, we expect it to be able to accommodate a wide variety of other ore types and processing methods with minimal or no changes. This system is also able to incorporate new circuits or sensors, as it is designed with such flexibility in mind. We also have the ability to process a wide range of feed materials/particle sizes, with in-house crushing equipment. The system is fully instrumented and controlled via a custom National Instruments LabVIEW PLC and is operated by trained engineers and technicians.